Fast Hole EDM Drilling into Carbide
Eroding Result: Process reliability & highest precision with AGEMA Machines
The following advantages result from erosive machining and Fast Hole EDM Drilling into carbide and steel on an AGEMA Start Hole Drilling EDM Machine.
Small hole EDM drilling due to a small spark gap. An electrode with a larger diameter can be used, which significantly improves accuracy in micro drilling.
No microcracks
No corrosion
No cobalt washout
Enables Sinker EDM & Fast Hole Drilling on one machine
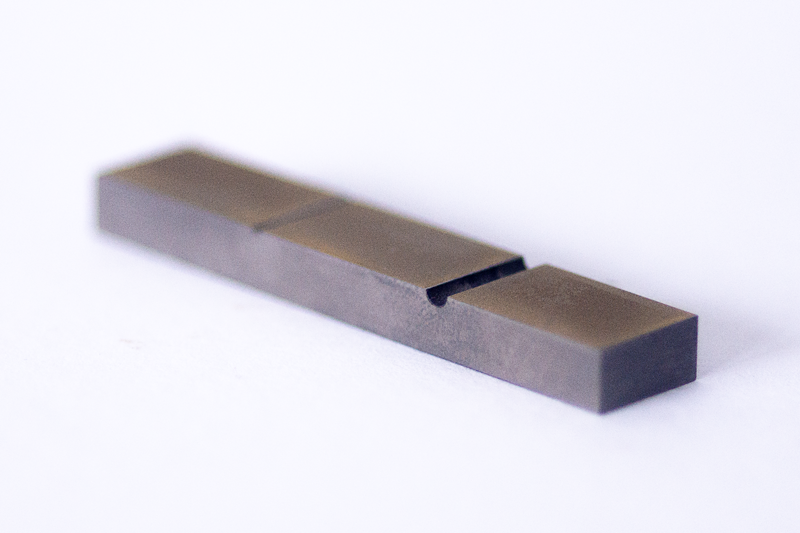
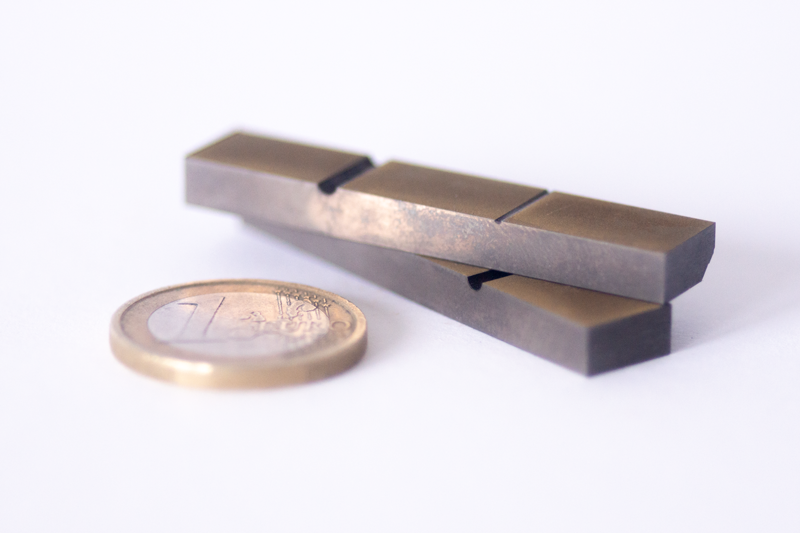

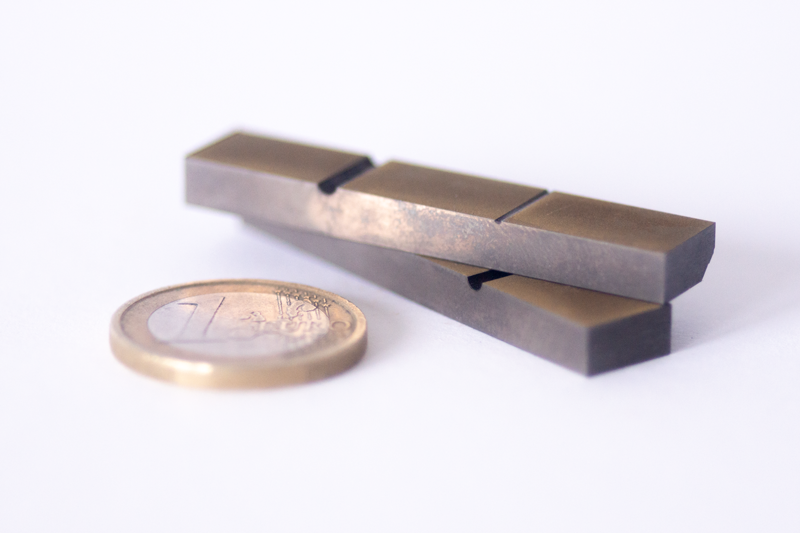
NON-DESTRUCTIVE GENERATION OF FAST HOLE EDM DRILLING
Through mineral oil as dielectric we achieve highest precision and quality in our eroding result in carbide and steel: Our used dielectric is an extremely thin liquid dielectric with the lowest possible surface tension. The dielectric is particularly suitable for work in the finest finishing area with a small spark gap, e.g. for micro-drillings or rather small hole EDM drilling and when eroding carbide and steel components in microelectronics.
A comparable surface quality is not possible with a deionized water machine.
Here is a comparision:
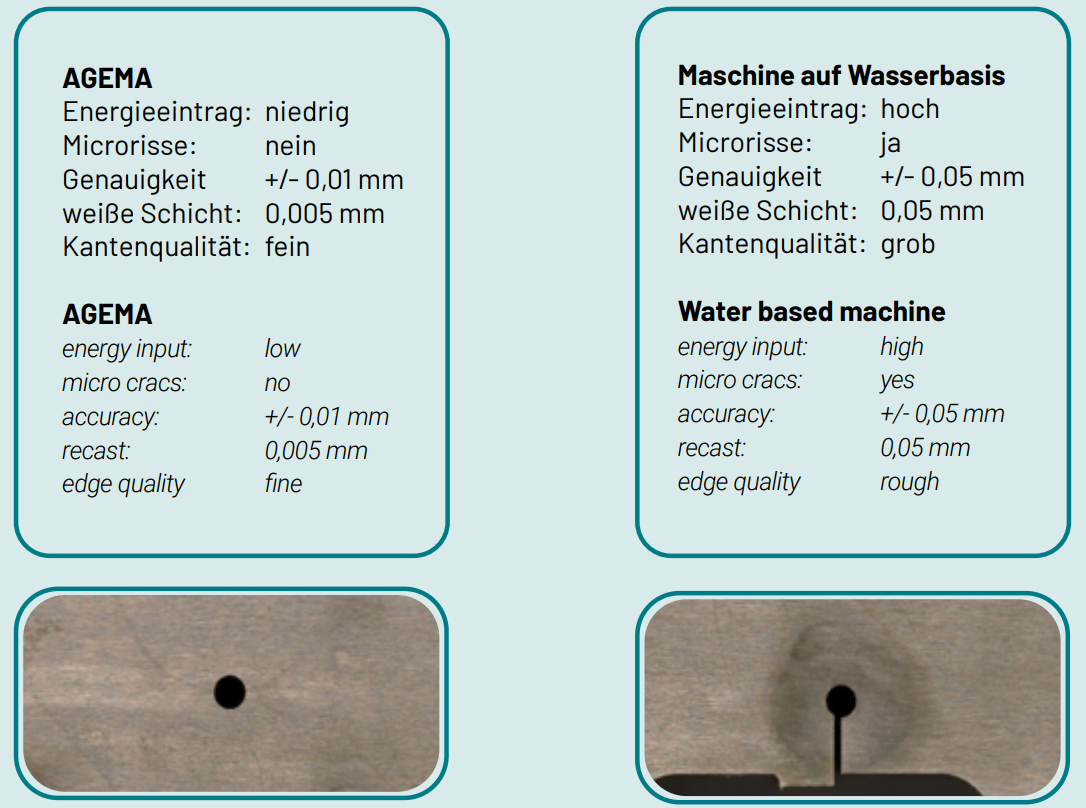
Comparison: Fast hole EDM drilling in carbide with water or oil?
There are significant differences in the quality of the EDM result when machining workpieces with a water or oil bath machine. Holes drilled with a water machine can show edge zone damage due to heat input into the workpiece. This is clearly visible in the white layer around the drilling in this photo.
Water-based erosion machines also require a larger erosion gap to achieve stable discharges. This introduces more energy into the workpiece, which can lead to stresses and damage in the component. As a result, the final diameter of the hole is also larger, as can also be seen in the photo.
1. Start hole EDM with a deionized water machine
2. Start hole EDM with oil dielectric on a AGEMA machine
Problems during the EDM process
Despite the maximum removal rate, structural changes and pitting should be avoided. Fundamental AGEMA concepts are high flashover strength, low viscosity, a good thermal conductivity and chemical stability even at the highest temperatures of the mineral oil-based dielectric. The use of this dielectric is only possible with the coordinated and gentle generator technology. Result: a comparable surface quality is not possible with a deionized water machine.
A larger electrode can also be used thanks to a small spark gap. This improves the accuracy of the drill holes. This comparison is illustrated once again here, Oil-based dielectric (first picture) against the electrode inside a water-based dielectric (second picture).
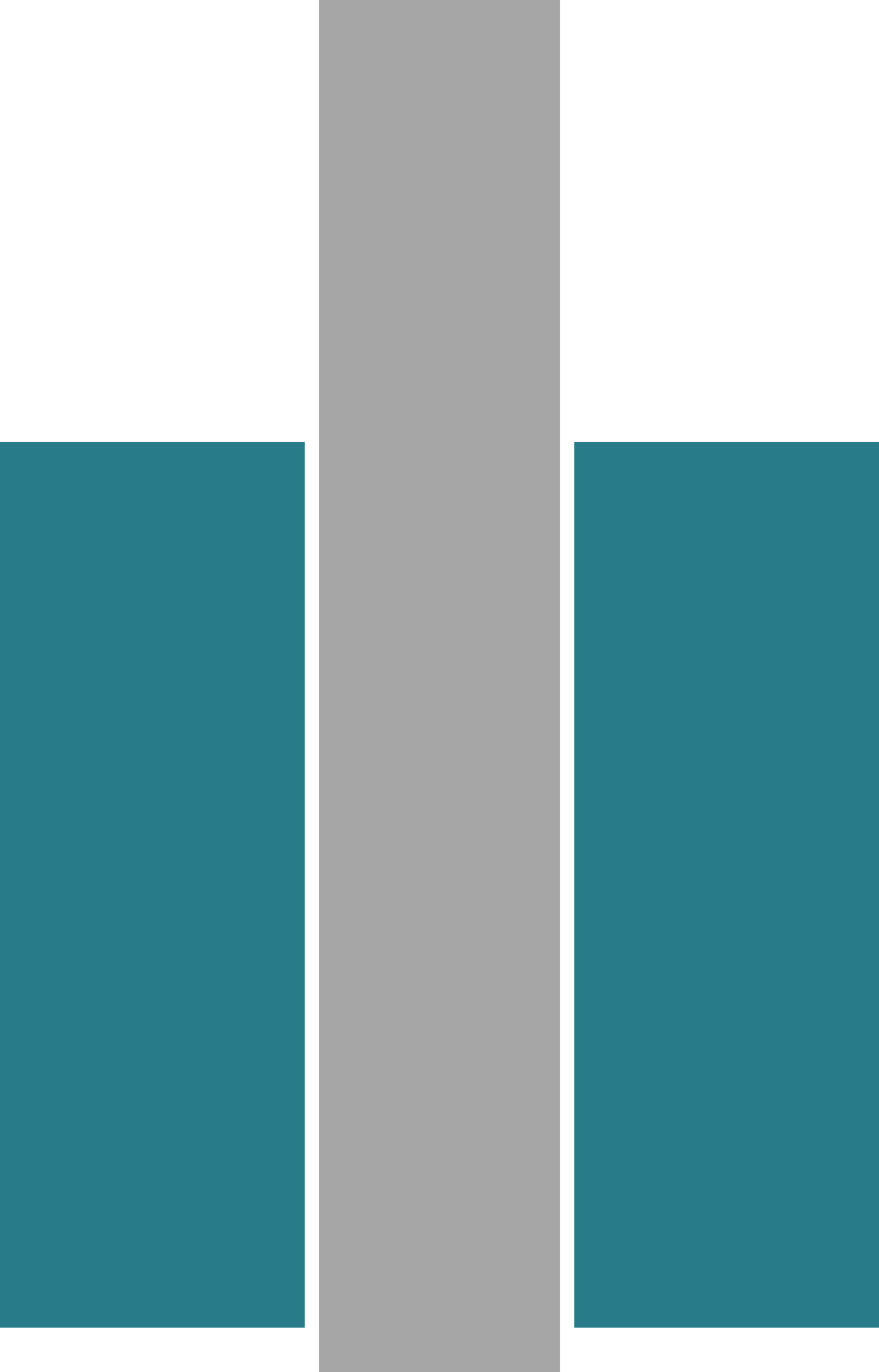

NON-DESTRUCTIVE GENERATION OF DRILLING HOLES
Fast Hole EDM Drilling into Carbide and Steel: We offer test processings.
We are happy to offer trials on your workpieces or test processings.
Contact us or or one of our international sales partners.